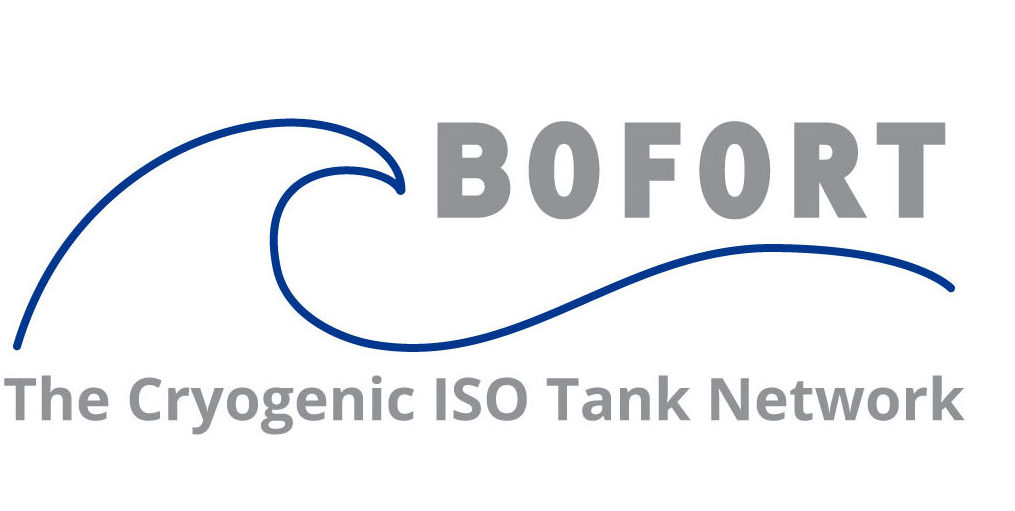
GEM TN-93-442
Recommended Leak Rates for the Extra Large Cryogenic Insulating Vacuum Vessels of the GEM Experiment Gerry Chapman
Superconducting Supercollider Laboratory
Derek Cragg Rutherford Appleton Laboratory –
Oxford July 26, 1993
RECOMMENDED LEAK RATES FOR THE EXTRA LARGECRYOGENIC INSULATING VACUUM VESSELS OF THE GEM EXPERIMENT AUTHORS: GERRY CHAPMAN – SSCL DEREK CRAGG *R.A.L*Rutherford Appleton Laboratory – Oxford (GB)
1.1 Overall Permissible Leak Rates for Ambient Temperature Vacuum Systems for vacuum systems operating at ambient temperature the permissible leak rate is the leak rate which will not interfere with the process being undertaken. This is normally taken to mean that the overall leak rate should not increase the required base pressure by more than 1 % e.g. in a system with a required base pressure of 1XI0-6mbar and pumped with a1000 litre/sec. high vacuum pump, the overall leak rate should not be < 1-6100.1000.10litre mbar/sec.i.e. IXI0-5 litre mbar/sec.
1.2 Permissible Leak Rates for Individual Leaks Difficulty is met in defining the maximum permissible size of any leak found as it include the actual number of leaks found on the system and the sum of all those leaks. If too high a figure for the permissible size is chosen and there are a larger number of leaks than has been budgeted for then the overall leak rate specification will be exceeded. This will result in either repairing enough of the larger leaks to meet the specification, leaving known leaks unrepaired, or revising the permissible individual leakrate downwards with the possibility, then of having to retest the whole system. This is very undesirable if the schedule is tight and both are unsound practices
A better approach is to examine Figure 1 which gives the distribution of leaks by size indifferent types of welded joint. This graph shows that virtually no leaks exist below the value lXl0-9 Std cc/sec. and less than three leaks in a thousand found will be less than the value lXlO-a Std cc/sec. It would be very nice to be able to specify a minimum permissible leak size of IXI0-9Std cc/sec. with the expectation of getting a leak free system. In real terms however this is not easy to do as the sensitivity of mass spectrometer leak detectors depends to a great extent on the cleanness of the component or system being tested.
Under what could be constructed as normal conditions inordinate amounts of time can be expended waiting for the item under test to be pumped clean enough so that the background level is low enough to detect leaks of lXI0-9 Std cc/sec. or lower. However, at leak detection levels of XI0-8 std cc/sec. things improve and with normal vacuum systems it is found to be possible to leak detect to this level on a consistent and reliable basis without large amounts of time being expended getting the background level of the mass spectrometer leak detector to a sufficiently low level.lXIO-a Std. cc/sec. is the recommended maximum permissible leak rate for an individual leak.
1.3 Air Leaks into the Insulating Vacuum of Cryogenic Systems
Figure 2 shows that above pressures of about lXl 04 mbar the heat leak due to gaseous conduction start to become appreciable and this pressure is used as a bench mark for the maximum permissible pressure in the insulating vacuum of a cryogenic system at anytime. In a breakdown situation it is wasteful in terms of re-start time and energy consumed to allow a cryogenic system to warm up or boil off cryogen more quickly if it can be prevented by what is ultimately good vacuum leak test procedures. The criterium then is that in a breakdown situation the leak rate on the system must be low enough that the pressure level never rises above lXIO6 mbar.In a lighting strike situation, likely to be prevalent in the Dallas area, there could be power outage of perhaps a week. Under these circumstances the maximum leak rate allowed on the outer vacuum vessel of the Barrel Krypton Calorimeter would bel.SXl0-6 Std cc/sec. and on the outer vacuum vessel of the End Cap Krypton Calorimeter the same leak rate would be 1. 3XI0-6 Std cc/sec. Incidentally these figures assume the system pressure before breakdown is about lXl 0-6mbar. You could not nm at lXIO 4 mbar, because any breakdown would put the pressure above this value.
1.4 Air Leaks into the Insulating Vacuum of cooled systems These systems fall into a different category because air from any external leaks is likely to be cryopumped on to the helium cooled surfaces before it can be pumped away by the- high vacuum pumps. ia superconducting solenoid quenches for any reason the liquid components can rise in temperature to a level where all the cryopumped evaporates. As before air evaporates. advantageous if under these circumstances the pressure in the system does not rise above lXIO4 mbar. A typical machine cycle could be nine months running with a three month shutdown. in the nine months running the solenoid should not accumulate enough cryopumped air to send the vacuum pressure over lXlO6 mbar in a fault/quench situation. On the GEM Solenoid this is equivalent to a leak rate of
7X10-6 Std cc/sec.
1.5 Leaks from cooled components into the insulating vacuum of cryogenic systems If all the leak testing is carried out at ambient temperatures it is not sufficient and moreover could be dangerous to use any overall leak rate criteria for ambient temperature vacuum systems on vessels which will operate at cryogenic temperatures and contain liquefied cryogens. Calculations show that all leaks at ambient temperature above a value of about lXI0-10Std cc/sec. are in a regime where viscous flow predominates. in this regime when a leak is exposed to liquid the leak rate will increase by a factor of over 150 for cryogens such as nitrogen and krypton and nearly 10,000 for helium. This latter figure assumes the helium does not enter the superfluid phase, if it does the increase in many orders of magnitude more.
1.6 Recommendations: The discussion on the effects of leaks into the insulating vacuum of cryogenic systems demonstrates that permissible leak rates into the insulating vacuum of cryogenic vessels is much lower than might be expected and that it is dangerous to fix an overall vacuum leak for any final global test if the vacuum testing is carried out at ambient temperature. It is the experience at International Laboratory’s over a period of 30 years that if all components in any vacuum system are leak tested to a level of lXl0-1 Std cc/sec. then itis unusual to end up with a system which has any leaks at all. All systems are routinely tested to this level and it has been found less time consuming to do this than to keep an inventory of all leaks found and perhaps go over a total leak rate limit which on a cryogenic system can at best be described as arbitrary. The recommendation is to follow the International Laboratory procedures and to test each component and the final system to the same level of 1×10-s Std cc/sec. Every effort should be made to test those components which operate at cryogenic temperatures under low temperature conditions. A simple way of doing this is to immerse the components in liquid nitrogen immediately prior to vacuum leak testing. It has been found through bitter experience that dye penetrate testing of welded vacuum joints is counterproductive. The dye penetrate prevents the carrying out of an effective repair and more important adds another process into the leak detection procedure. Experience shows that mass spectrometer leak detection is quicker and more effective than any other leak detection procedure.1.7 Leak Test Specification The leak test specification for cryogenic equipment should include the following points:• The leak detector will be a mass spectrometer tuned to helium gas and be capable of detecting leaks down to the !XI o-io Std cc/sec. level.
• The mass spectrometer will be set up so that it will detect leaks down to lXl0-1Std cc/sec.
• Leaks of this size should give a full scale deflection or equivalent on the indicating instrumentation.
• In order to obtain instant readiness for leak testing and large deflections on the indicating instrumentation of the mass spectrometer the ratio of the pumping speed to the volume of the system should be as large as possible. 300/sec. is a good target value for routine testing.
• All leaks found will be repaired.
• The final test of the system as a whole will be the same as that for individualleaks.4CJl.